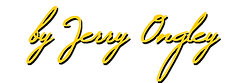
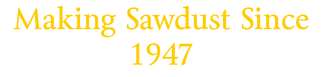

Some Things Just Take Time...
Below I have outlined the steps in turning a Cherry bowl. Most woods provide similar challenges, while some are much more complicated but often rewarding such as walnut, American elm and palm, to name a few.
Southern cherry tends to have a greater distinction between heartwood and sapwood. The heartwood being a dark pink to red color and the sapwood being white to almost a watermelon rind color. The Southern Cherry has an abundance of gum pockets and is mostly used in the production of kitchen cabinetry and craft type products.

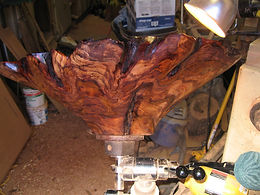

The Process
Although the wood is selected with a shape or size in mind, the “blank” often dictates its own shape! The blank is cut into a circle for mounting on the lathe. Usually there is considerable work in “rounding” the blank to prevent the inevitable vibration. Vibration results from an out of round shape or different densities through-out the blank.
After mounting the blank on a faceplate, a foot (the little hollow area), is created on the bottom of the piece. The underside of the piece is completely “turned” using various tools, sanded and usually receives two to three coats of finish. The piece is now reversed on the lathe and mounted on or by the newly created “foot”.
The interior of the bowl is often the most difficult part of turning. If the piece is large then there is much wood to be extracted. Often times if a lathe tool makes a “catch” in the wood at this time it will cause the entire piece to fly off of the lathe and bounce around the shop striking anything in its way. At speeds between 700-1000 Rpm’s, person turning is not exempt from "catching" a flying bowl when least expected and therefore shop safety is observed at all times and a requirement. The very first bowl I ever turned came off the lathe and hit me on the forehead.
Generally, due to the instability of the wood, especially if there are cracks, voids, bark intrusions, and/or other objects to contend with, much of the finishing has to be done by sanding. Occasionally the final stages are accomplished only by hand sanding.
When the piece has evolved sufficiently, approximately three coats of finish are applied. The finish of choice is Tung Oil and hand rubbed with a light sanding between coats. Tung Oil penetrates and protects the bowl and gives it a nice appearance while enhancing the color of the wood. This may or may not be followed with a coat or two of a good quality wax.



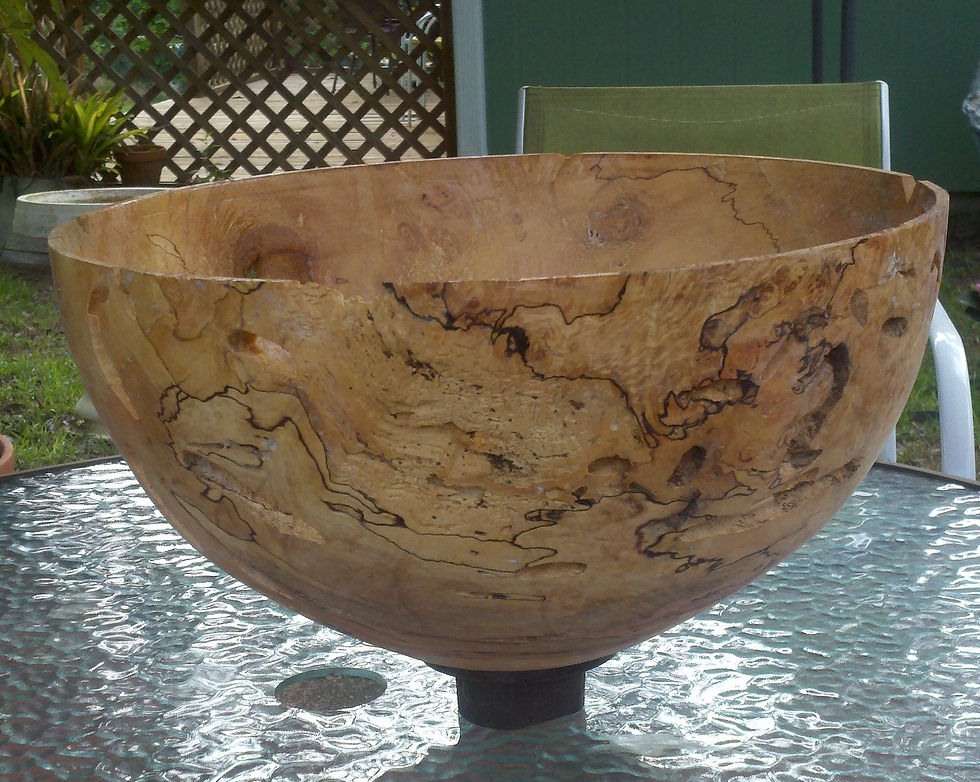







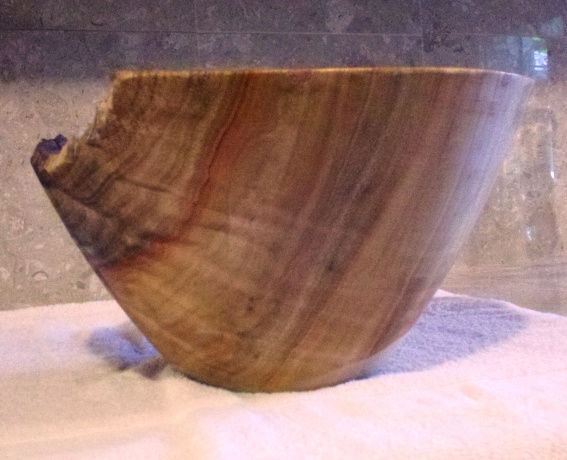